Liquid silicone rubber (LSR) molding offers several advantages that make it an excellent choice for various projects:
- Precision and Detail: LSR molding allows for intricate designs and precise molding of complex shapes. This makes it suitable for projects requiring high precision and detailed components.
- Consistency: LSR molding offers excellent consistency in the finished products. It ensures uniformity in dimensions, surface finish, and material properties across multiple parts, which is crucial for many applications.
- Versatility: LSR can be molded into a wide range of shapes, sizes, and geometries, making it versatile for various applications across industries such as automotive, medical, electronics, and consumer goods.
- High-Quality Finished Products: LSR molding produces high-quality finished products with excellent clarity, durability, and resistance to extreme temperatures, chemicals, and environmental factors.
- Fast Production Cycle: LSR molding processes are typically fast, allowing for high-volume production within short lead times. This makes it suitable for projects with tight timelines or high production demands.
- Cost-Effectiveness: While the initial tooling costs for LSR molding may be higher compared to other molding processes, it offers long-term cost benefits due to its efficiency, consistency, and minimal waste during production.
- Biocompatibility: LSR is often used in medical and healthcare applications due to its biocompatibility, making it suitable for products such as medical implants, prosthetics, and wearable medical devices.
- Chemical Resistance: LSR exhibits excellent resistance to chemicals, making it suitable for applications where exposure to harsh chemicals or solvents is a concern.
Overall, choosing LSR molding for your project can result in high-quality, precise, and cost-effective production of components with versatile applications across various industries.
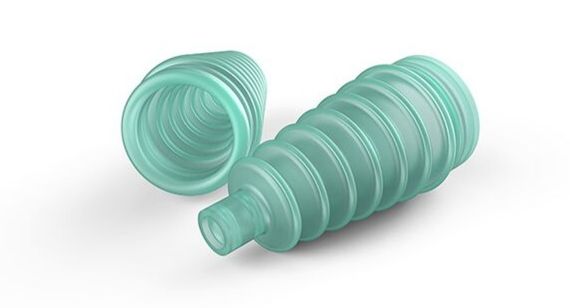
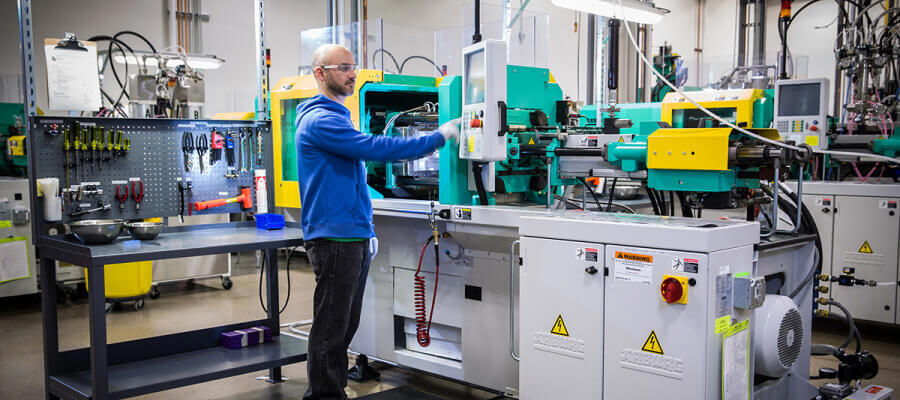