Have you ever wondered how the surfaces of certain objects achieve that smooth, glossy finish that seems almost seamless? Imagine a raw, slightly rough 3D-printed part transforming into a polished, refined piece with no visible layer lines. This process doesn’t involve sandpaper or intensive handwork but instead relies on a method called vapor polishing.
Vapor polishing is a technique utilized in the finishing of various materials, particularly plastics like polymethyl methacrylate (PMMA), also known as acrylic. It’s a chemical process that involves exposing the surface of the material to a vaporized solvent. The solvent interacts with the surface, causing it to slightly melt and reflow, erasing imperfections and creating a sleek, glossy finish.
This method is commonly employed in industries where a high-quality, polished appearance is essential, such as in manufacturing, prototyping, and product design. The vapor polishing process ensures not only aesthetic enhancement but also improves the material’s mechanical properties, making it stronger and more durable.
Keeping up with the significance of achieving impeccable finishes in the realm of product manufacturing and design, vapor polishing serves as a game-changer. It offers an efficient and effective means to elevate the quality and visual appeal of the final product without extensive manual labor.
How does Vapor Polishing Work?
Vapor polishing relies on the principle of solvent action. The process occurs in a controlled environment where the material is exposed to a solvent vapor, typically acetone or methanol. The solvent interacts with the surface of the material, causing a controlled, selective dissolution of the outer layer. This dissolution effectively erases imperfections, creating a glossy, smooth finish.
The key here is precision and control. The duration of exposure and the concentration of the solvent vapor must be carefully calibrated to achieve the desired finish without compromising the structural integrity of the material.
What Materials Benefit from Vapor Polishing?
Primarily used for thermoplastics like acrylic, polycarbonate, and ABS (Acrylonitrile Butadiene Styrene), vapor polishing is highly effective in enhancing the appearance of 3D-printed parts made from these materials. The technique is particularly advantageous for parts with intricate geometries or those produced via additive manufacturing, as it can reach and refine even the most intricate details.
Advantages of Vapor Polishing
Beyond its aesthetic benefits, vapor polishing offers several advantages:
- Efficiency: It’s a relatively quick process compared to manual polishing methods.
- Consistency: Provides a uniform finish across the entire surface.
- Strengthens Materials: Enhances the structural integrity of the material.
- Cost-Effectiveness: Reduces the need for labor-intensive finishing techniques.
Is Vapor Polishing Environmentally Friendly?
While vapor polishing is an effective and efficient method, it’s essential to address its environmental impact. The process involves the use of solvents, which can raise concerns about air quality and waste management. However, advancements in technology aim to mitigate these issues by developing eco-friendly solvent options and implementing closed-loop systems that recycle solvent vapor.
Conclusion
In the realm of manufacturing and design, achieving a flawless finish is often as crucial as the structural integrity of the product itself. Vapor polishing stands as a testament to innovation in refining surfaces, offering a swift, efficient, and cost-effective means to transform raw materials into sleek, polished products with impeccable aesthetics. As technology evolves, the pursuit of even more environmentally friendly and efficient vapor polishing methods continues, promising a future where quality meets sustainability in surface finishing techniques.
Feel free to share this guide with anyone curious about the transformative power of vapor polishing in manufacturing and design processes!
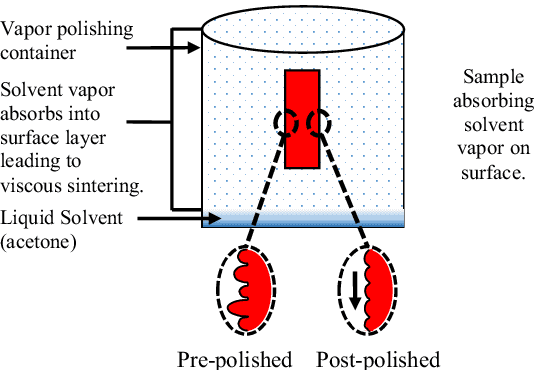