Have you ever wondered what makes precision machining truly exceptional? How does the surface finish of a machined part affect its functionality? Let’s embark on a journey to uncover the significance of surface roughness in CNC machined products.
Surface roughness in machining refers to deviations from an ideal surface texture that result from the machining process. It’s the measure of finely spaced surface irregularities, showcasing the quality and precision of a machined part. These irregularities, often microscopic, profoundly impact a component’s performance, durability, and aesthetics.
Machined parts with precise surface finishes exhibit enhanced functionality, reduced friction, and improved resistance to wear and corrosion. The quest for optimal surface roughness is paramount in achieving superior product quality and performance.
Surface roughness isn’t just about aesthetics; it’s a critical aspect that directly influences a product’s functionality and lifespan. Imagine a meticulously designed component with flawed surface roughness—its efficiency compromised, durability questioned, and potential lifespan diminished.
Why does Surface Roughness Matter in CNC Machining?
Surface roughness profoundly impacts functionality and performance in machined products. It affects how two surfaces interact, influences friction coefficients, and determines a part’s ability to withstand environmental conditions and stressors.
How is Surface Roughness Measured in Machined Products?
In precision machining, surface roughness is quantified using parameters like Ra (Average Roughness), Rz (Maximum Height), and Rt (Total Roughness). These measurements provide engineers and manufacturers with precise data on a part’s surface quality, aiding in quality control and adherence to design specifications.
Does Surface Roughness Affect Product Cost and Durability?
Yes, surface roughness impacts both cost and durability. Finer surface finishes often require more meticulous machining processes, influencing production costs. However, these finely finished parts typically exhibit improved durability and functionality, justifying the investment.
How Can Engineers Optimize Surface Roughness in Machined Parts?
Engineers can employ various techniques such as adjusting cutting parameters, tool selection, and utilizing advanced machining technologies like CNC machining. These strategies help achieve desired surface finishes while balancing efficiency and cost-effectiveness.
Maintaining optimal surface roughness is a collaborative effort between manufacturers, engineers, and designers. It’s a testament to precision and quality, ensuring machined parts meet stringent standards and perform flawlessly in their intended applications.
Conclusion
Understanding surface roughness in machining is pivotal for engineers, manufacturers, and anyone involved in product development. It’s not merely about aesthetics but a fundamental aspect influencing a product’s functionality, durability, and overall performance. Achieving the perfect surface finish isn’t just an art; it’s a science that elevates the quality of machined products to exceptional levels.
I hope this covers the depth and importance of surface roughness in CNC machined products, shedding light on its significance in engineering and manufacturing.
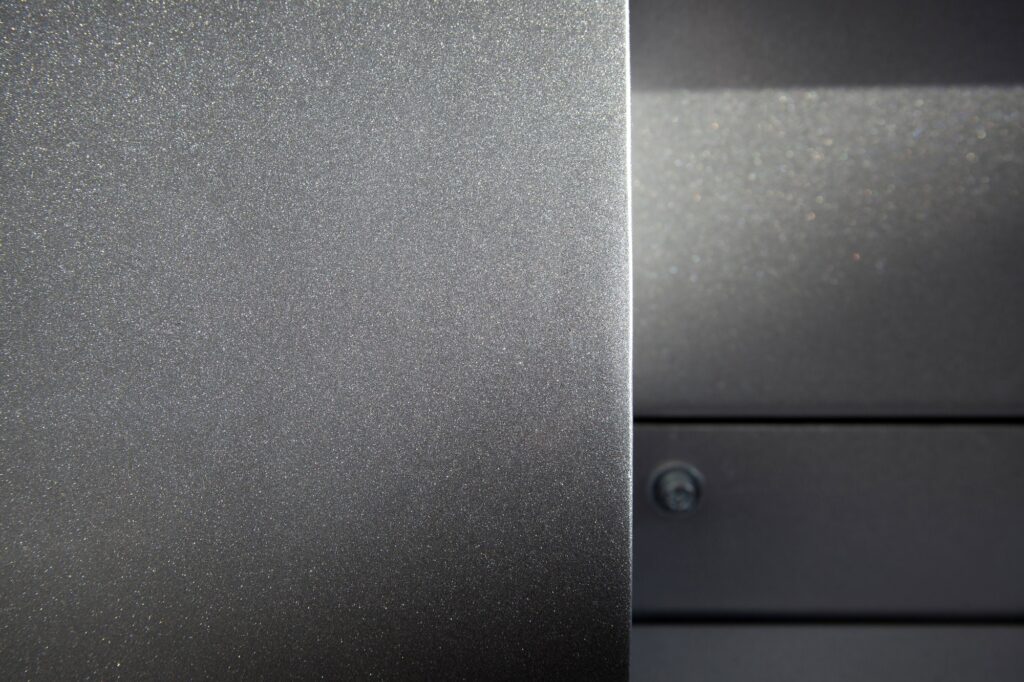