As an industry expert at MIMCNC, specializing in precision metal parts, I’m thrilled to take you on a journey through the world of texture surfaces in CNC machining. In this comprehensive listicle, we’ll dive into several common texture surfaces, explore their applications, and provide valuable insights to help you make informed decisions when selecting the right surface finish for your precision metal parts.
1. The Significance of Texture Surfaces
Before we delve into specific texture surfaces, let’s understand why surface finish matters in CNC machining. Texture surfaces play a pivotal role in determining the functionality, aesthetics, and performance of your metal parts. The choice of surface finish can impact factors such as friction, corrosion resistance, and even the overall look of the product.
The table below outlines the key attributes associated with various texture surfaces and their applications:
Surface Finish | Attributes | Applications |
---|---|---|
Smooth Finish | Low Ra value (smooth) | Aerospace components, medical devices, optical equipment |
Brushed Finish | Uniform directional grain pattern | Kitchen appliances, automotive trim, decorative components |
Bead-Blasted Finish | Fine matte texture, improved corrosion resistance | Electronic enclosures, firearm components, architectural details |
Anodized Finish | Enhanced corrosion resistance, vibrant color options | Consumer electronics, sports equipment, automotive parts |
Polished Finish | Mirror-like surface, high reflectivity | Jewelry, luxury watches, artistic sculptures |
Textured Finish | Raised or indented patterns | Grip-enhancing surfaces on tools, industrial equipment |
2. Smooth Finish
Introduction: A smooth finish is characterized by a low Ra value, indicating a surface that is free of irregularities and imperfections. It’s achieved through precision machining and careful polishing, resulting in a sleek and refined appearance.
Applications: Smooth finishes find their place in industries where aesthetics and performance are paramount. Aerospace components, medical devices, and optical equipment benefit from the low friction and corrosion resistance of smooth surfaces.
Summary: When you need precision and a pristine look, a smooth finish is the way to go. It combines functionality with a visually appealing surface.
3. Brushed Finish
Introduction: The brushed finish is known for its uniform, directional grain pattern. It’s achieved by brushing the metal surface with abrasive materials, creating a distinct texture that adds a touch of elegance.
Applications: Brushed finishes are often seen on kitchen appliances, automotive trim, and decorative components. They provide a stylish and tactile surface that resists fingerprints and scratches.
Summary: If you desire a surface that’s both visually appealing and resistant to wear, consider a brushed finish for your metal parts.
4. Bead-Blasted Finish
Introduction: Bead blasting involves propelling fine glass beads at the metal surface to create a fine matte texture. This process improves corrosion resistance and can hide minor imperfections in the metal.
Applications: Bead-blasted finishes are commonly found on electronic enclosures, firearm components, and architectural details. The texture provides an attractive yet functional surface.
Summary: For metal parts that need to withstand harsh environments while maintaining an appealing appearance, a bead-blasted finish is an excellent choice.
5. Anodized Finish
Introduction: Anodizing is an electrochemical process that enhances the corrosion resistance of metal surfaces while offering a wide range of color options. It creates a durable, oxide layer on the metal’s surface.
Applications: Anodized finishes are prevalent in consumer electronics, sports equipment, and automotive parts. The added layer of protection and color customization make them versatile.
Summary: When you require both aesthetic appeal and superior corrosion resistance, an anodized finish allows you to achieve both in one package.
6. Polished Finish
Introduction: A polished finish is the epitome of shine and reflectivity. This process involves extensive polishing and buffing to create a mirror-like surface.
Applications: Jewelry, luxury watches, and artistic sculptures often feature polished finishes. The high reflectivity adds a touch of luxury and sophistication.
Summary: If your metal parts demand a level of elegance and brilliance, a polished finish can turn them into true works of art.
7. Textured Finish
Introduction: Textured finishes involve the creation of raised or indented patterns on the metal surface. These patterns can serve functional purposes, such as improving grip.
Applications: Textured finishes are ideal for grip-enhancing surfaces on tools and industrial equipment. They provide tactile feedback and enhance usability.
Summary: When functionality is paramount, and you need a surface that enhances usability, a textured finish can make your metal parts more user-friendly.
In conclusion, selecting the right texture surface for your CNC machined metal parts is a crucial decision that impacts both form and function. Each type of finish offers unique attributes that cater to specific applications and preferences. At MIMCNC, we understand the importance of texture surface, and our commitment to quality and precision ensures that your metal parts will meet and exceed your expectations, no matter which finish you choose.
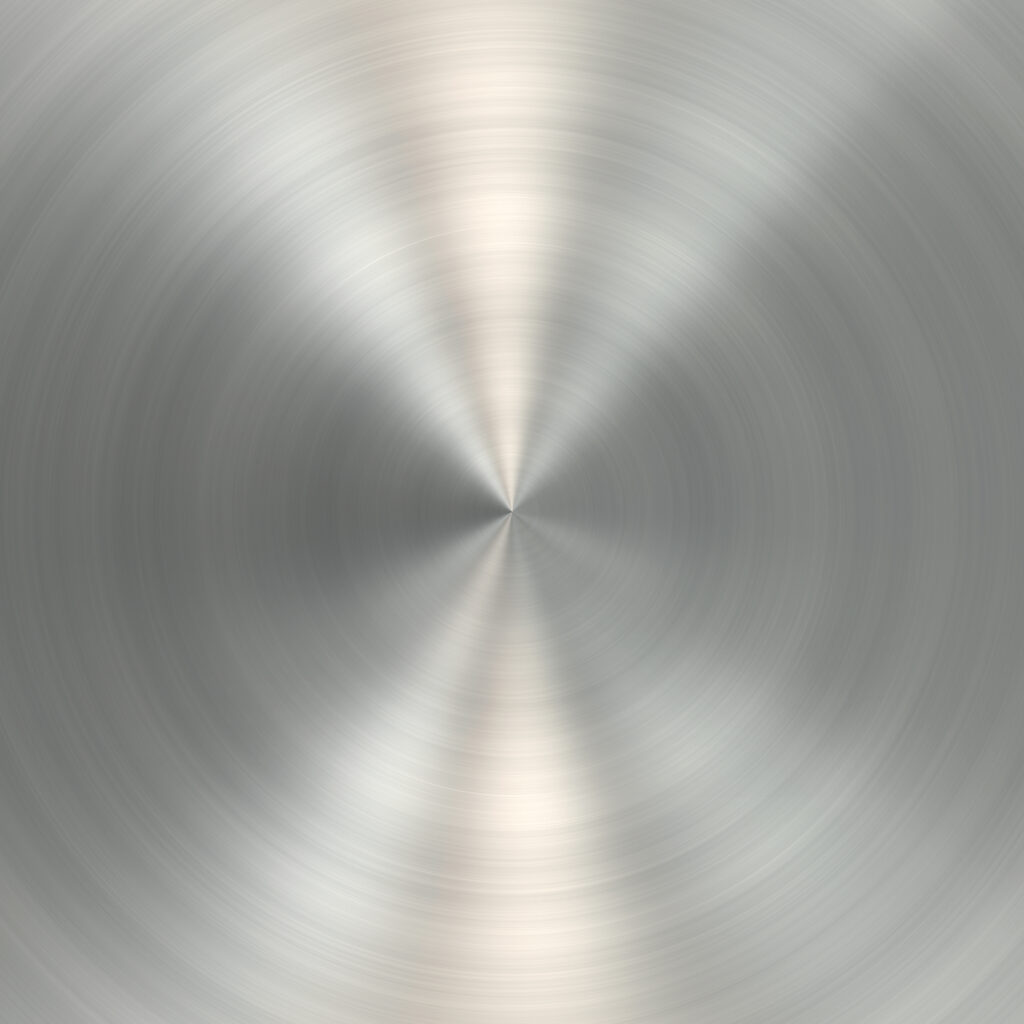