Liquid Silicone Rubber (LSR) is an advanced material known for its exceptional thermal resistance, making it an ideal choice for applications requiring durability under high temperatures. Below are some key aspects of why LSR “takes the heat” and its advantages:
Key Thermal Properties:
- High-Temperature Resistance:LSR can typically withstand temperatures ranging from -50°C to 250°C (-58°F to 482°F) without losing its mechanical or physical properties.Specialty grades can perform in even higher temperature ranges.2.
- Thermal Stability:Unlike many other elastomers, LSR maintains its flexibility, resilience, and sealing properties under prolonged exposure to high heat.
- Low Compression Set: Retains its shape and elasticity even after being subjected to high temperatures and mechanical compression.4
- Flame Retardancy: Certain grades of LSR are inherently flame-resistant or can be modified to meet flame retardancy standards like UL 94 V-0.
- Advantages in High-Heat Applications:
Non-Toxic and Chemically Stable: LSR does not release harmful gases when exposed to heat, making it suitable for sensitive applications like medical devices and food-grade products.
Hydrophobic Nature: Its water-repellent surface ensures performance in high-humidity environments even at elevated temperatures.
Resistance to Degradation: LSR resists oxidative degradation, making it durable in harsh thermal cycles and UV exposure.
Applications:
Automotive: Used for gaskets, O-rings, and other components exposed to engine heat and harsh chemicals.
Consumer Electronics: Ideal for seals and keypads in devices that generate significant heat.
Medical Devices: Autoclavable seals and components for sterilization processes.
Industrial: Insulators, connectors, and seals for machinery operating under high temperatures.
Would you like more details on specific LSR grades or manufacturing techniques like injection molding?
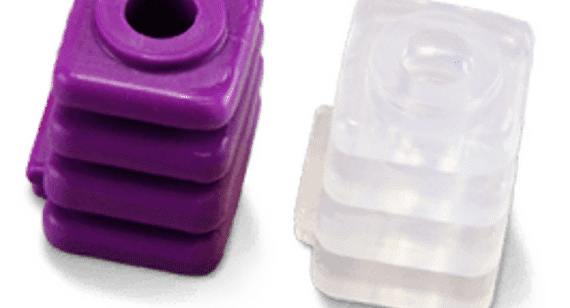