Liquid Silicone Rubber (LSR) Molding Process
Liquid Silicone Rubber (LSR) molding is a highly efficient manufacturing process used to produce precision parts from liquid silicone rubber, a versatile elastomer. It’s used in a variety of industries such as medical devices, automotive, electronics, and consumer products. Below is a breakdown of how LSR molding works:
- Material Preparation
Liquid Silicone Rubber (LSR): LSR comes in a two-part system: Part A (the base material) and Part B (the curing agent or catalyst). These two components are mixed together just before injection. The material is liquid and can flow easily, which allows it to fill complex molds.
Coloring: Pigments can be added to the LSR if color is needed, though the material is typically clear or translucent in its natural state. - Mold Design
Mold Material: LSR molds are typically made of high-grade metal, such as aluminum or steel, which can withstand the high pressures and temperatures involved in the molding process.
Mold Design: The molds are designed with precise cavities for the part being produced. The mold may also contain vents for air to escape during the injection process. - Injection Process
Molding Machine: A specialized LSR injection molding machine is used, which consists of two main parts: the injection unit and the clamping unit. The injection unit is responsible for mixing and injecting the LSR into the mold, while the clamping unit holds the mold halves together under pressure.
Injection: The mixed LSR material is injected into the mold cavities under high pressure. Because LSR is liquid, it flows into all areas of the mold, ensuring that even complex geometries are filled properly. - Curing (Vulcanization)
Heat Application: Once the LSR is injected into the mold, the mold is heated to a specific temperature (usually around 170-200°C or 338-392°F). This activates the curing agent in Part B of the silicone, which causes the material to undergo a chemical reaction known as vulcanization.
Cross-Linking: During vulcanization, the liquid silicone undergoes a cross-linking process that turns it into a solid, flexible rubber-like material. This process typically takes a few minutes to complete, depending on the size and complexity of the part. - Cooling and Ejection
Cooling: After the part is fully cured, the mold is cooled to a temperature where it is safe to handle. This allows the LSR to solidify and hold its final shape.
Ejection: Once cooled, the mold is opened, and the finished part is ejected. The part is then inspected for quality and any excess material, such as flash (extra silicone that has leaked out of the mold cavity), is trimmed off. - Post-Processing (Optional)
Trimming and Inspection: Parts may undergo additional post-processing steps such as trimming excess material or performing quality checks to ensure the part meets specifications.
Sterilization (For Medical Parts): In industries such as medical device manufacturing, parts may undergo sterilization after molding to ensure they are free of contaminants.
Advantages of LSR Molding:
Precision and Accuracy: LSR molding allows for high-precision parts with tight tolerances, making it ideal for industries like medical devices and electronics.
High Volume Production: Once the mold is created, LSR molding is highly efficient for producing large quantities of parts quickly.
Excellent Material Properties: LSR has excellent durability, flexibility, temperature resistance, and biocompatibility (for medical applications).
Complex Geometries: The liquid nature of LSR allows it to fill even intricate molds, producing parts with complex shapes that may be difficult or impossible with other methods.
Biocompatibility: LSR can be formulated to meet stringent medical standards, making it ideal for medical device applications.
Disadvantages of LSR Molding:
Initial Tooling Costs: The initial cost of creating the molds can be expensive, though this is offset by the high efficiency and low cost per part in mass production.
Material Cost: LSR is more expensive than some other rubber or plastic materials, although its durability and high performance can justify the cost.
Limited to Silicone: The molding process is designed specifically for silicone materials, so it cannot be used for other types of elastomers or plastics.
Applications of LSR Molding:
Medical Devices: Catheters, seals, gaskets, medical tubing, and implants.
Consumer Products: Baby bottle nipples, kitchenware, wearable devices, and seals for appliances.
Automotive: Seals, gaskets, and vibration dampers.
Electronics: Keypads, switches, and seals for electronic devices.
In summary, LSR molding is a highly effective method for producing high-quality, durable, and flexible silicone parts, especially for applications that require precision, biocompatibility, or high-volume production. The process is cost-effective in mass production, but the initial setup cost can be high.
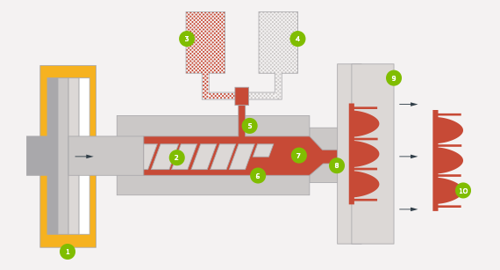