As someone deeply involved in the precision machining industry, I understand the critical role that polishing plays in achieving the highest quality metal parts. Polishing isn’t just about aesthetics; it’s about ensuring the functionality, durability, and performance of the components we produce at MIMCNC. In this comprehensive guide, I will walk you through the ins and outs of polishing, sharing insights, tips, and resources to help you make informed decisions for your projects.
Polishing 101: The Basics
Before diving into the nitty-gritty details, let’s start with the basics of polishing. Essentially, polishing is the process of refining a metal surface to achieve a smooth, shiny, and pristine finish. This finish not only enhances the appearance of the product but also plays a crucial role in its overall performance. Here’s a quick overview of the key aspects:
1. Types of Polishing
Polishing can encompass various methods, each suited for different materials and finishes. The most common types include:
- Mechanical Polishing: This method involves using abrasives, such as sandpaper or polishing wheels, to physically remove imperfections from the surface.
- Electrolytic Polishing: Often used for metals like stainless steel, this process involves immersing the material in an electrolyte solution and applying an electric current to achieve a smooth finish.
- Chemical Polishing: Chemicals are used to dissolve the surface layer of the material, leaving a polished surface behind. This method is highly effective for achieving mirror-like finishes.
2. Importance of Polishing
Why does polishing matter in the world of precision machining? Let’s break it down:
- Surface Smoothness: Polishing removes micro-roughness, ensuring a smoother surface. This is crucial for reducing friction and wear in moving parts.
- Corrosion Resistance: A polished surface is less susceptible to corrosion, which is especially vital for components exposed to harsh environments.
- Enhanced Appearance: Polishing enhances the visual appeal of metal parts, making them more attractive to customers and end-users.
- Improved Functionality: Precision components often require tight tolerances, and polishing helps maintain these critical dimensions.
Listicle Item 1: The Science Behind Polishing
Polishing is not just a superficial process; it involves a deep understanding of material properties, abrasives, and techniques. Here’s a deeper dive into the science of polishing:
Material Compatibility
Different metals and alloys require specific polishing methods. For instance, stainless steel and aluminum have distinct properties, and choosing the wrong approach can result in subpar results. Always consider the material when planning your polishing process.
Abrasive Selection
The choice of abrasive material and grit size is crucial. Finer abrasives yield smoother finishes, but they may take longer to achieve the desired result. Coarser abrasives, on the other hand, can remove imperfections quickly but may leave visible scratches.
Surface Preparation
Before polishing, proper surface preparation is essential. This includes cleaning the material thoroughly to remove contaminants and ensuring that any prior machining marks are addressed. A clean canvas ensures a more effective polishing process.
Techniques and Equipment
The technique and equipment used in polishing can vary widely. Hand polishing is suitable for small, intricate parts, while larger components may require automated polishing machines. Understanding which method is best for your project is key to success.
Measuring Results
Quality control is integral to polishing. Employ measurement tools like calipers, micrometers, or optical comparators to ensure that the finished product meets the required specifications.
Listicle Item 2: Achieving Different Finishes
Polishing isn’t a one-size-fits-all process. Different finishes serve various purposes and aesthetic preferences. Here are some common finishes you might encounter:
Mirror Finish
A mirror finish is the pinnacle of polishing, creating a surface so smooth that it reflects like a mirror. It’s often used in decorative applications, where aesthetics are paramount. Achieving this finish requires meticulous polishing and buffing.
Satin Finish
A satin finish strikes a balance between matte and glossy. It provides a slightly textured appearance while maintaining some reflectivity. This finish is popular for products where a sophisticated look is desired.
Brushed Finish
Brushed finishes create a pattern of fine, parallel lines on the surface. This finish is not only visually appealing but also helps mask minor imperfections. It’s often used in applications where wear and tear are expected.
Matte Finish
Matte finishes have a non-reflective, dull appearance. They are excellent for reducing glare and are commonly used in applications like instrument panels or scientific equipment.
Custom Finishes
Polishing allows for endless possibilities in creating custom finishes to meet specific design requirements. This can include textured patterns, logos, or unique surface treatments.
Listicle Item 3: Benefits of Precision Polishing
Now that we’ve covered the fundamentals let’s delve into why precision polishing is a game-changer in the precision machining industry:
Improved Functionality
Precision polishing ensures that critical dimensions are maintained within tight tolerances. This is essential for components that require precise fits and clearances, such as aerospace or medical devices.
Extended Lifespan
Polishing reduces surface roughness, which, in turn, reduces wear and friction. Components that undergo precision polishing tend to have a longer lifespan and require less maintenance.
Enhanced Corrosion Resistance
Corrosion is the enemy of metal parts, especially those used in harsh environments. Precision polishing removes surface imperfections that can be entry points for corrosive agents, making the component more resistant to degradation.
Aesthetic Appeal
In industries where visual aesthetics matter, precision polishing can make products stand out. Whether it’s consumer electronics, automotive parts, or architectural components, a polished finish can elevate the perceived quality of a product.
Superior Performance
In applications like automotive engines or industrial machinery, components that have undergone precision polishing often perform better due to reduced friction and improved material properties.
Listicle Item 4: Challenges and Solutions
While precision polishing offers numerous benefits, it’s not without its challenges. Here are some common issues you might encounter and how to address them:
Surface Contamination
Contaminants can negatively impact the polishing process. Ensure that your workspace is clean, use proper cleaning agents, and consider working in a controlled environment to minimize contamination.
Material Hardness
Polishing extremely hard materials can be time-consuming and challenging. Choose abrasives and techniques specifically designed for hard materials to achieve the desired results efficiently.
Consistency
Maintaining consistency in the polishing process is crucial for quality control. Implement standard operating procedures (SOPs) and conduct regular checks to ensure that all components meet the same high standards.
Cost Management
Precision polishing can be an investment, but the long-term benefits often outweigh the initial costs. Work closely with your polishing provider to find cost-effective solutions without compromising quality.
Listicle Item 5: The Role of Technology
Technology plays a significant role in modern precision polishing. Here are some advancements that have revolutionized the industry:
CNC Machining
Computer Numerical Control (CNC) machining has transformed precision polishing. It allows for highly precise and automated polishing processes, reducing human error and improving consistency
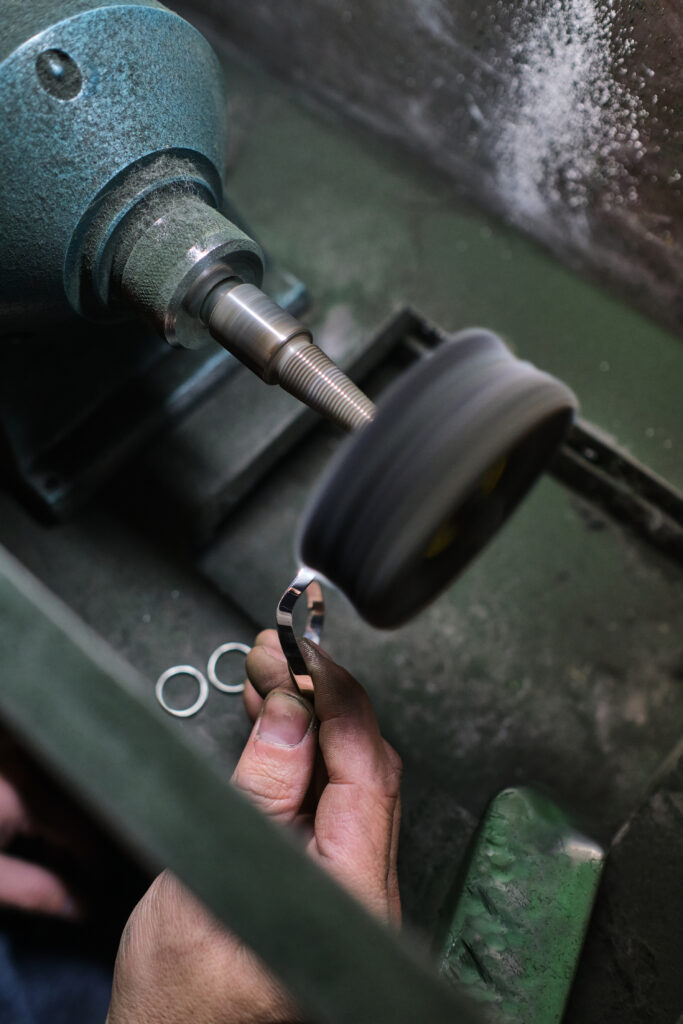