CNC machining and die casting are two widely used manufacturing processes with distinct characteristics and applications. When it comes to producing precision metal parts, understanding the differences between these techniques becomes crucial. In this blog post, we will explore CNC machining and die casting, comparing their key aspects to help you make an informed decision about which process suits your needs.
CNC Machining: Precision at Your Fingertips
CNC machining, short for Computer Numerical Control machining, is a subtractive manufacturing process that involves removing material from a solid block to shape it into the desired form. This process utilizes computer-controlled machines with rotating cutting tools to carve out the intricate details of the part.
CNC machining offers several advantages:
- Precision and Accuracy: CNC machining provides exceptional precision and accuracy, allowing for tight tolerances and intricate designs. It ensures consistent quality and repeatability, making it suitable for industries where precision is critical.
- Versatility: This manufacturing process can work with a wide range of materials, including metals like aluminum, stainless steel, titanium, and even engineering plastics. It offers flexibility in material selection to meet specific project requirements.
- Customization and Prototyping: CNC machining is well-suited for producing custom parts and prototypes. Its ability to work directly from digital designs enables rapid prototyping and design modifications, ensuring that the final product meets the client’s exact specifications.
- Low to Medium Volume Production: CNC machining is ideal for low to medium volume production runs, making it an excellent choice for businesses that require smaller batches of precision parts.
Die Casting: Efficiency in Mass Production
Die casting is a high-pressure manufacturing process that involves injecting molten metal into a steel mold cavity. Once the metal solidifies, the mold is opened, and the finished part is removed. Die casting is particularly suitable for producing complex shapes with a high level of detail.
Here are some key advantages of die casting:
- High Efficiency: Die casting enables high-volume production, making it an efficient choice for businesses that require large quantities of parts. The process can achieve rapid cycle times, allowing for increased productivity and shorter lead times.
- Complex Geometry: Die casting can produce parts with intricate details and complex geometries, including thin walls, sharp corners, and fine features. This process is well-suited for applications that demand intricate designs and precise specifications.
- Cost-Effective for Mass Production: Once the initial tooling costs are covered, die casting becomes a cost-effective option for large-scale production. The per-unit cost decreases significantly as the volume increases.
- Material Versatility: Die casting offers a wide range of materials to choose from, including various metals and alloys. Aluminum, zinc, and magnesium are commonly used in die casting due to their favorable characteristics.
CNC Machining vs Die Casting: Which One to Choose?
Now that we have explored the key features of CNC machining and die casting, let’s address some commonly asked questions to help you decide which process is better suited for your manufacturing needs:
Can CNC machining achieve the same level of complexity as die casting?
CNC machining can achieve high complexity and precision, allowing for intricate designs and tight tolerances. However, die casting has an advantage when it comes to producing parts with extremely complex geometries and thin walls, thanks to the capability of the mold to replicate intricate details.
Is die casting more cost-effective for large production runs?
Die casting is generally more cost-effective for large production runs due to its high efficiency and shorter cycle times. Once the initial tooling costs are covered, the per-unit cost decreases significantly, making it a favorable option for mass production.
Can CNC machining provide greater material versatility?
CNC machining offers a broader range of material options, including metals, engineering plastics, and composites. Die casting is limited to materials suitable for the casting process, such as aluminum, zinc, and magnesium alloys. If your project requires materials outside the scope of die casting, CNC machining provides more flexibility.
Conclusion
In conclusion, both CNC machining and die casting have their unique advantages and applications. CNC machining excels in precision, versatility, and adaptability, making it ideal for low to medium volume production runs, customization, and prototyping. On the other hand, die casting offers high efficiency, cost-effectiveness in mass production, and the ability to produce complex geometries.
When choosing between CNC machining and die casting, consider factors such as the desired part complexity, production volume, lead time requirements, material options, and budget constraints. It is advisable to consult with experienced manufacturing professionals who can assess your specific needs and guide you toward the most suitable manufacturing process for your project.
Regardless of which process you choose, embracing modern manufacturing techniques will undoubtedly enhance your product development and help you deliver high-quality precision parts to your customers efficiently.
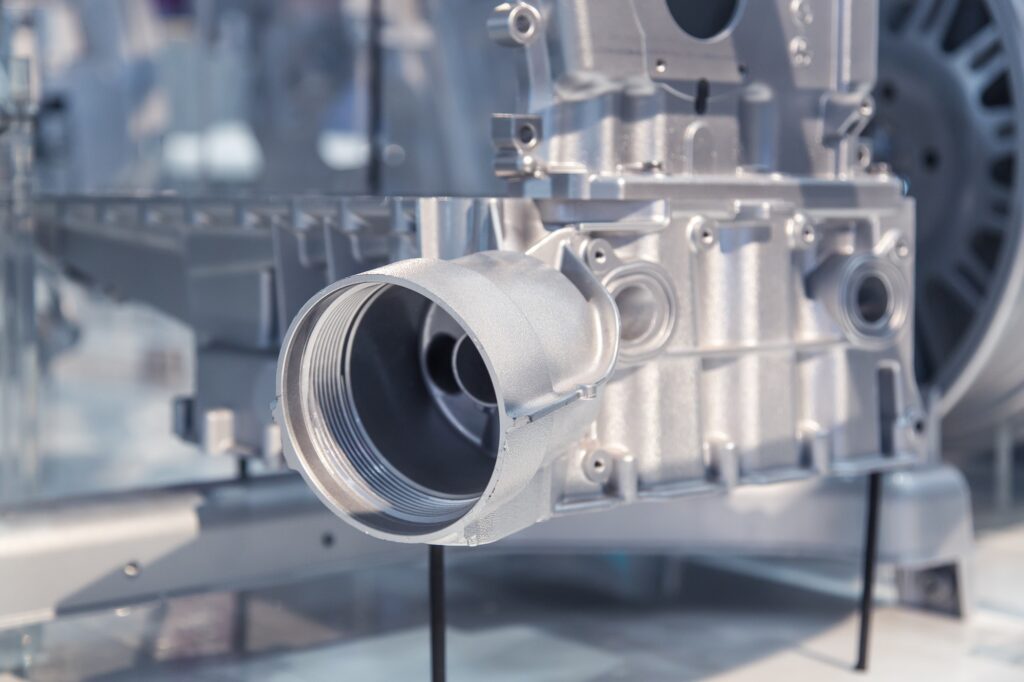