As an expert in the field of precision machining, I have the qualifications to provide you with valuable insights and solutions for complex design challenges in this industry. In this article, I will share 10 effective solutions that can help you overcome the complexities involved in the design of metal and plastic machined parts. Let’s dive in!
1. Understanding Material Properties and Selection
To ensure the success of your design, it’s crucial to have a deep understanding of the properties of different materials. Factors such as strength, durability, heat resistance, and chemical compatibility play a significant role in the selection process. For metal parts, materials like aluminum, steel, and titanium offer various advantages based on the specific requirements of your project. Similarly, for plastic parts, materials such as ABS, polycarbonate, and nylon possess distinct characteristics suitable for different applications.
2. Collaborating with Experienced Design Engineers
Partnering with experienced design engineers who specialize in metal and plastic machining can greatly benefit your project. These professionals possess the technical expertise and knowledge to optimize your design for manufacturability. By involving them early in the design process, you can leverage their insights to create efficient and cost-effective parts.
3. Utilizing Advanced CAD/CAM Software
Modern Computer-Aided Design (CAD) and Computer-Aided Manufacturing (CAM) software enable precise modeling and simulation of complex part designs. These tools help you visualize the final product, identify potential issues, and optimize the design before production begins. CAD/CAM software also facilitates seamless communication between designers, engineers, and manufacturers, ensuring a smooth workflow and reducing the chances of errors.
4. Applying Design for Manufacturability (DFM) Principles
Design for Manufacturability (DFM) principles involve designing parts with the manufacturing process in mind. By considering factors such as material selection, tooling, machining techniques, and tolerances during the design phase, you can significantly reduce production costs and improve efficiency. Collaborating with manufacturers who are well-versed in DFM practices will further enhance the success of your design.
5. Optimal Tooling Selection and Optimization
The selection and optimization of tooling play a crucial role in achieving accurate and efficient machining. Different tool materials, coatings, and geometries are available for various applications. Working closely with tooling experts can help you choose the right tools for your project, considering factors such as material hardness, surface finish requirements, and production volume.
6. Implementing Multi-Axis Machining
Complex part designs often require intricate features that can be efficiently machined using multi-axis CNC machines. These machines offer enhanced flexibility and precision by enabling simultaneous movement of the cutting tool along multiple axes. Leveraging the capabilities of multi-axis machining can help you achieve intricate geometries and tight tolerances, even for highly complex designs.
7. Utilizing Rapid Prototyping Technologies
Rapid prototyping technologies, such as 3D printing, allow you to quickly validate and iterate your designs before moving into full-scale production. With the ability to produce functional prototypes using a wide range of materials, including both metals and plastics, rapid prototyping accelerates the development process and helps identify potential design flaws early on.
8. Incorporating Design for Assembly (DFA) Principles
Design for Assembly (DFA) principles focus on simplifying the assembly process and reducing the number of components required. By optimizing the design for ease of assembly, you can streamline production, minimize costs, and enhance the overall quality of the final product. Collaborating with manufacturers experienced in DFA practices can help you achieve efficient and cost-effective assembly processes.
9. Implementing Quality Control Measures
Maintaining consistent quality throughout the production process is essential for complex part designs. Implementing rigorous quality control measures, such as dimensional inspections, surface finish analysis, and material testing, ensures that the final products meet the specified requirements. Partnering with manufacturers who have robust quality control systems in place will give you confidence in the reliability of your machined parts.
10. Continuous Communication and Collaboration
Effective communication and collaboration between designers, engineers, and manufacturers are key to the success of any complex part design project. Regularly sharing updates, addressing design challenges, and seeking feedback from all stakeholders involved will help streamline the entire process and ensure that the final product meets or exceeds expectations.
Summary
Designing complex metal and plastic machined parts requires a combination of technical expertise, collaboration, and utilization of advanced technologies. By understanding material properties, collaborating with experienced design engineers, utilizing CAD/CAM software, and following DFM and DFA principles, you can optimize your designs for manufacturability. Leveraging multi-axis machining, rapid prototyping, and implementing quality control measures further enhance the overall success of your project. Remember, continuous communication and collaboration are essential for a seamless workflow and the delivery of high-quality machined parts.
With these 10 solutions at your disposal, you are well-equipped to tackle the challenges associated with complex design in the metal and plastic machining industry.
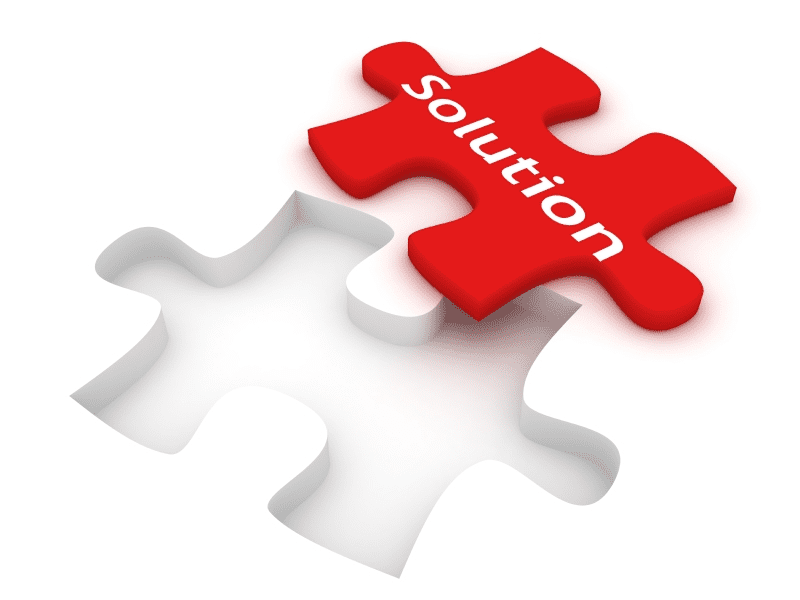