At MIMCNC, we take pride in crafting customized precision metal parts for our valued clients. In this listicle, I’ll share ten invaluable tips for designing machine parts that not only meet but exceed your expectations. Whether you’re a seasoned engineer or just getting started in the field, these tips will help you make informed decisions and ensure the success of your CNC machining projects.
Tip 1: Understand Your Material Options
Before diving into the design process, it’s crucial to have a comprehensive understanding of the materials available for CNC machining. Different materials offer distinct properties, such as strength, durability, and conductivity. Aluminum, stainless steel, and brass are popular choices for their versatility. Consult material datasheets and consider factors like thermal expansion and conductivity to make an informed selection. Online resources like MatWeb provide extensive material data to guide your decision.
Tip 2: Prioritize Design for Manufacturability (DFM)
A successful CNC machining project begins with Design for Manufacturability (DFM). This means creating designs that are optimized for the manufacturing process, reducing complexity, and minimizing the risk of errors. Employ geometric tolerancing, use standard tool sizes, and avoid sharp internal corners to streamline production. Embrace CAD software like SolidWorks or AutoCAD for easy DFM integration into your designs.
Tip 3: Embrace 2D and 3D CAD Modeling
2D and 3D CAD modeling is the backbone of precision CNC machining. These tools allow you to visualize your designs comprehensively and ensure every detail aligns with your project goals. Autodesk Fusion 360, Rhino, and SolidWorks are excellent software choices for precise modeling. Invest time in mastering these programs to maximize the potential of your designs.
Tip 4: Optimize Tolerances
When it comes to CNC machining, tolerances are paramount. Tight tolerances ensure the accuracy and precision of your machined parts. However, overly tight tolerances can drive up production costs. Strike a balance by understanding your specific requirements and industry standards.
Tip 5: Consider Toolpath Efficiency
Efficient toolpaths can significantly impact machining time and costs. Leverage CAM (Computer-Aided Manufacturing) software to generate optimized toolpaths. CAM software, such as Mastercam or CAMWorks, provides efficient toolpath strategies, reducing material waste and minimizing tool wear.
Tip 6: Don’t Overlook Surface Finish
Surface finish is often an underestimated aspect of CNC machining. It affects not only aesthetics but also functionality. Select the appropriate surface finish for your application, whether it’s smooth, textured, or polished.
Tip 7: Design with Assembly in Mind
If your project involves multiple machined parts coming together, design with assembly in mind. Ensure that tolerances, fastener placements, and alignment features allow for smooth and error-free assembly. CAD software can assist you in simulating assembly processes and identifying potential issues.
Tip 8: Test Prototypes and Iterations
Prototyping is a crucial step in CNC machining product design. It allows you to validate your design, assess functionality, and identify potential flaws. Use rapid prototyping techniques like 3D printing or order prototype parts to test your design’s feasibility and functionality before proceeding to mass production.
Tip 9: Communicate with Your CNC Machining Partner
Collaboration with your CNC machining partner is essential. Engage in open communication to convey your design requirements, tolerances, and expectations clearly. Discuss feasibility, material options, and potential improvements. A transparent and collaborative relationship with your machining partner, like MIMCNC, ensures a smoother production process.
Tip 10: Stay Updated on Industry Trends
The field of CNC machining is continually evolving. To stay ahead of the curve, invest time in researching industry trends, new materials, and cutting-edge technologies. Join industry forums, attend trade shows, and read publications like Modern Machine Shop to stay informed about the latest developments.
In conclusion, designing precision CNC machining products requires a blend of technical knowledge, creativity, and attention to detail. By following these ten expert tips, you can create designs that are not only manufacturable but also cost-effective and high-performing. Remember that CNC machining is a collaborative effort, and maintaining open communication with your machining partner is key to achieving outstanding results. Stay curious, embrace new technologies, and keep refining your design skills to excel in the world of precision machining. Your typical client, like Michael, will appreciate your dedication to quality and reliability in every project.
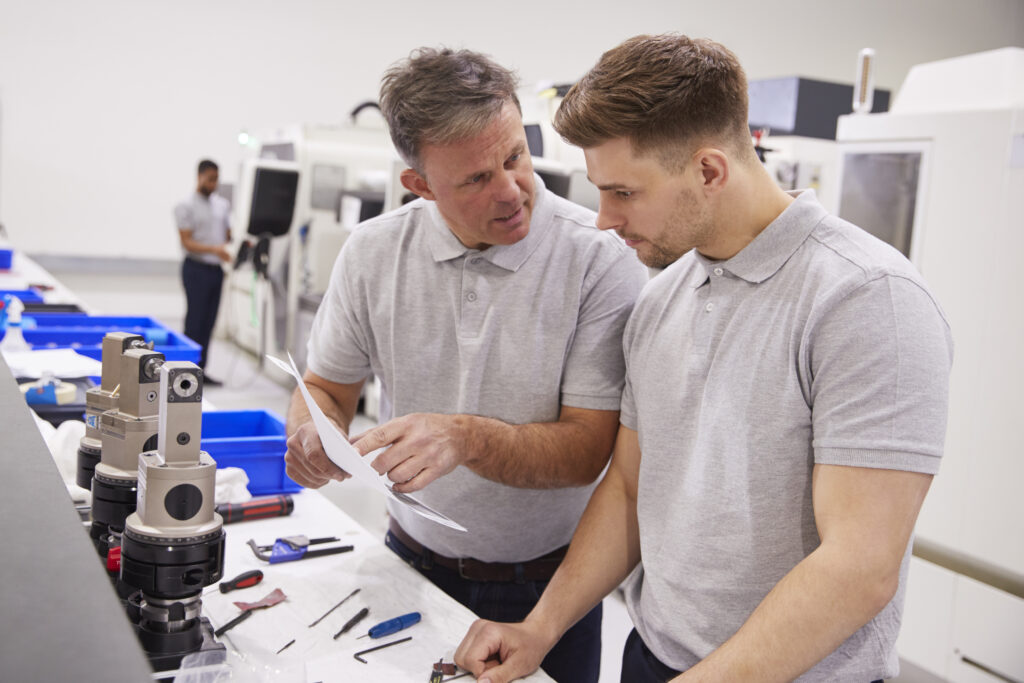